支援実績紹介:品質改善・リードタイム短縮・5S改善
2021.01.30
工場の品質改善実施事例です。工程の不良ゼロ達成!生産効率アップなど、工場の改善事例を紹介します。
当社のこだわり! 一緒に悩み考える、問題解決請負業に徹します。
1.不良流出ゼロ達成でお客様の信頼を勝ち取った!
中国 SMT基板組み立て工場の品質改善、出荷検査ラインの設定
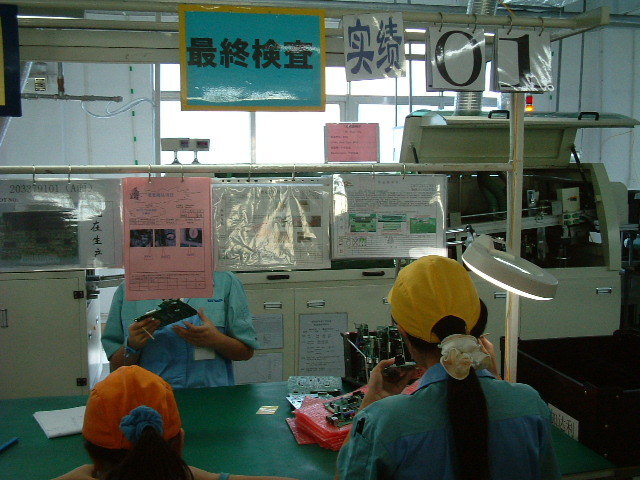
■ 時期 2006年~2007年
■ 改善要望 顧客流出クレーム多発、不良の流出防止対策
■ 問題点 作業ミス多発、検査漏れの問題判明
■ 解決方向 作業者教育認定制度創設、出荷検査ライン新設
■ 導入手法 正しいFTA分析/正しいなぜなぜ分析/体系的4M変更管理/信賞必罰制度
不良が激減したため、納入先より大変喜ばれ、信頼を取り戻すことが
できました。大変感謝しております。
2.多品種小ロット生産工場のリードタイム短縮1/2達成!
受注設計型製品の空調設備製造工場の生産ライン改善
■ 時期 2013年1月~6月 ■ 改善要望 生産ライン効率化 リードターム短縮化 ■ 問題点 生産計画、進捗、不良内容が可視化されていない、問題が潜在化
■ 解決方向 生産ラインの流れ明確化、見える化、5S改善、キーマン教育
■ 導入手法 体系的4M変更管理、5S3定改善、見える管理、レイアウト改善
日本式の品質管理手法を習得できました。これをきっかけに
社員の意識が変化し、率先して改善を行うようになりました。
3.セル生産方式導入により生産性30%アップ!
韓国 大型電子装置組立工場の生産ライン改善
■ 時期 2014年6月~継続中
■ 改善要望 生産量増加に伴い管理体制強化、組立ラインの効率化、在庫削減を図る
■ 問題点 仕掛在庫が多い、リードタイム長い、改善活動は停滞
■ 解決方向 全社改善プロジェクト結成、組み立てラインのセル化推進、キーマン教育
■ 導入手法 正しいプロジェクト改善活動、セル生産方式、多能工化、見える管理
フロアーの生産性は向上しました。これを工場全体に広げていきたいです。
セル生産方式の効果を実感しました。
5.売れるしくみ構築で新製品の販売額15%アップ
香川県 精米工場の生産効率化、間接業務改善、売れる仕組み構築
■ 時期 2014年8月~2017年2月
■ 改善要望 利益体質への転換、組織の見直し、業務マニュアルの体系整備
■ 問題点 限りある人材の有効活用、市場縮小の中、米を扱った新商品開発の
困難さ
■ 解決方向 営業部門組織の役割の明確化、5S改善活動、業務フロー作成
キーマン教育
■ 導入手法 小規模企業向け品質マネジメントシステム、正しい改善活動、
組織化・組織図、業務フロー
職場が大変きれいになり、働きやすくなりました
社員が増えても、昔ながらの個人商店の風土が抜けきらず
非効率な仕事のやり方になっていました。今回のご指導に
より管理のしくみが構築でき、仕事がやり易くなりました。
6.モノと情報の流れを改善、仕掛在庫の削減・リードタイム短縮
群馬県 プレス工場の生産性10%向上、リードタイム半減化
■ 時期 2019年7月~2020年4月
■ 改善要望 生産性向上により赤字経営からの脱却したい
■ 問題点 プレス工程~溶接工程までの複数工程間に仕掛在庫が滞留している
■ 解決方向 ネック工程基準の生産計画と進捗管理方式を採用、作業のムダ取り
キーマン教育
■ 導入手法 トヨタ生産方式の7つのムダ削減、TOC理論による生産管理方式
機種が多いため、それぞれのラインで、同様の対策を継続的に
実施し、相乗効果で赤字脱却を図りたいと思います。
7.成形工場 協業ロボット導入支援(補助金申請)
群馬県 プラスチック成型工場の生産性向上、リードタイム短縮